Downtime’ is one of the most dreaded words in manufacturing. While production downtime is part of life in a factory, managers, operators, and technicians constantly strive to reduce it and mitigate its effects.
When manufacturers have a decent understanding of their operation, usually this downtime is accounted for as "planned" downtime.
Planned downtime is the expected and predictable time required for changeovers, setups, tool changes, routine machine maintenance, and other tasks. It’s usually figured into capacity and production plans based on set standards and can be optimized through best practices and standard operating procedures.
But it’s unanticipated downtime that requires urgent and immediate action. It's unplanned manufacturing downtime that is unpredictable and must be addressed immediately (if not prevented altogether!). And there are many manufacturing downtime reasons to tackle.
Let's dive into tracking, measuring, and reducing your unplanned manufacturing downtime.
What is Unplanned Downtime?
Unplanned production downtime occurs when there is an unexpected disruption or failure of a machine or process. It increases costs, threatens promised delivery of finished goods, and often causes downstream problems that magnify its consequences.
There are many reasons for unplanned manufacturing downtime, including:
- Equipment failure
- Tool failure
- Operator error
- Poor maintenance
- Stockouts/inventory issues
- Poor planning
- Lack of communication
- Unoptimized changeover and setup processes
- Material staging/WIP
These manufacturing downtime reasons can be significantly improved. MachineMetrics can automatically notify team members of a downtime event. This can be used to deliver a notification to a tablet placed at the machine, a text message to a cell phone, an email, or even be used to automatically create work orders in a CMMS.
How to Measure Unanticipated Downtime
Before understanding how to reduce unplanned downtime, you must first measure it. Unplanned manufacturing downtime can be calculated based on lost time or lost revenue dollars. By tracking time, managers can review the reasons for it and develop strategies for process improvement to prevent the event from occurring as frequently or at all. By tracking dollars, companies see the impact on the cost of the product and its impact on revenue.
The formula for calculating unplanned machine downtime using a time measure is:
Unplanned Downtime = (Time Asset is Down / Total Time) x 100
This measurement can be applied to individual spindles, machines, shifts, departments, or factories depending on the level of focus needed by the person reviewing the data.
Calculating non-scheduled downtime as a cost may vary significantly from a few hundred dollars to tens of thousands of dollars per hour, depending on the operation’s size, complexity, and the number of workers impacted. The formula for calculating unanticipated downtime for lost dollars is:
Cost of Unplanned Downtime = Average Hourly Wage x (Time Asset is Down/Total Time) X Number of Employees Affected
Other things can easily add to the total cost of unanticipated downtime if the cost of overhead and other variables are included.
How to Reduce Unplanned Downtime
Reducing and eliminating unplanned downtime is an achievable goal, but the degree of success depends on the method and technology used. Below are a few actionable ways to get started.
Conduct Process Audits
You can't eliminate unanticipated downtime unless your processes are optimized. Process audits bring to light areas for improvement that will reduce or eliminate causes of unplanned manufacturing downtime.
Customers of ours often find that there is low-hanging fruit here. For example, moving tools closer to machines, or ensuring that material is available when it begins to run out.
Manual methodologies will bring some improvement but will struggle as it will be difficult to truly understand unplanned downtime in manufacturing and where inefficiencies exis
You'll end up spending a lot of time manually collecting machine production downtime events, writing down part counts, estimating cycle times...then putting the data into excel to understand where gaps exist...and then doing it all again next week.
A machine monitoring platform can collect and analyze data to deliver actionable insights in real-time for immediate action. This allows people to make more accurate decisions, rather than using gut instinct.
With accurate production data in hand, you can run a number of analyses to determine where issues and opportunities exist within your processes:
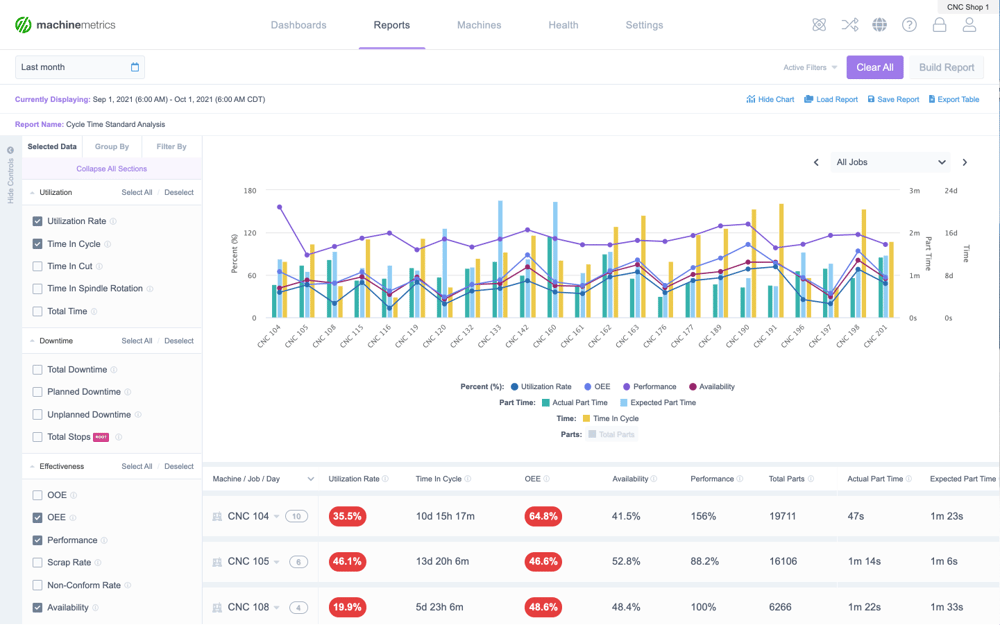
Use and Improve Standard Work
Standard work is a proven method for systemizing processes, operator motion, and other variables within production. Using standard work to ensure everyone is working the same way reduces unplanned machine downtime significantly.
MachineMetrics can automatically update important metrics that play a part in standard work and standard operating procedures. For example, we can send updated part counts and cycle times to an MES, ERP, or wherever else jobs are managed.
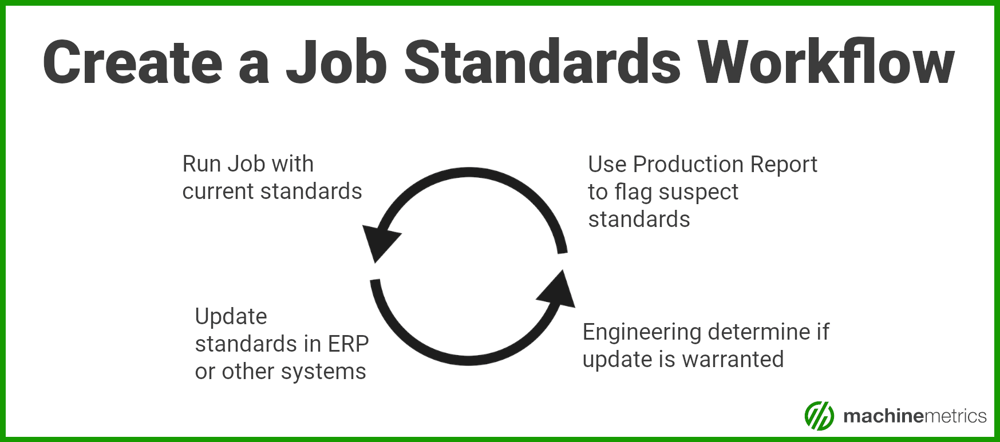
Develop Proactive Maintenance Strategies
Preventive maintenance was considered a giant leap from reactive maintenance, but it was only partial progress. While it resulted in lower unplanned manufacturing downtime, it wasn’t optimized for preventing production downtime and still resulted in under or over-maintenance that kept machinery idle.
With MachineMetrics, proactive, data-driven analysis empowers condition-based and predictive maintenance strategies. This allows for maintenance only when it is needed and also helps to ensure well-planned maintenance stops coincide with changeovers.
Implement Factory Monitoring
All of the above improvements are possible with manual methods, but they have inherent issues such as errors and bias and are labor-intensive. A machine data platform brings all these capabilities under one umbrella with real-time unsiloed data provided by your machines.
MachineMetrics also integrates with enterprise software such as ERP, MES, CMMS, and quality software to deliver real-time data and supercharge their native capabilities.
Real-time production dashboards above the shop floor provide immediate visibility into the status of machines.
Using Machine Data to Reduce Unplanned Downtime
Your machine data is the most valuable asset in reducing unplanned production downtime. With a production monitoring platform like MachineMetrics, accurate equipment data can be collected, standardized, and used in real-time.
For example, you could set up notifications whenever a machine goes down. This could automatically notify an operator or manager of a machine downtime event.
You could take this even further by tracking specific machine conditions that indicate a machine failure. For example, you could track coolant levels with a sensor. When coolant levels are getting low, an operator could be notified immediately, allowing them to resolve the issue.
Plug-and-play Machine Connectivity
Comments