Every manufacturing company wants to reduce changeover time. The changeover process may take days or weeks in some industries and only a few minutes in others. In industries where small lots or single pieces are produced, reducing regular changeover times through continuous improvement programs, SMED (Single-Minute Exchange of Die), and standard work can significantly boost efficiency and equipment utilization.
What is Changeover Time?
Changeover time is the total time elapsed between the last good part of the previous run and the first good part of the following run. The first piece of the following run must meet quality standards and specifications. “Dial-in” time must also be included in changeover time.
There’s an important distinction between internal and external changeover times. Internal changeover times represent the lapsed time described above. External changeover time is the time spent by operators, technicians, and other staff preparing for the change.
External changeover time variables can affect the total internal changeover time. For example:
-
Materials may be staged nearby to reduce waiting
-
A machine tool may be readied for addition to a carousel
-
Specialized staff may be stationed nearby to help with the change or check specifications
Since these variables have an impact on the internal changeover time, they can help to reduce it.
How to Measure Changeover Time
Traditional measurements of changeover time involved pen and paper and the ubiquitous clipboard. Stop and start times were recorded and included in daily production. Many companies took changeover time a step further by requiring task breakdowns within changeover time. These included factors such as:
- Cleaning
- Material change
- Measuring and setup
- Calibration
- Maintenance
- First run of good material
- Quality checks
The problem with these categories is that the more manual the process was, the less accurate the data was; numbers were often excluded, rounded, or omitted. These categories are best recorded and captured when downtime is automated.
Plug-and-play Machine Connectivity
Regardless of the method, several factors should be included in downtime calculations:
Lost Labor Cost – Labor is one of the most significant expenditures for any manufacturing company. Lost labor is calculated by the total number of hours lost or expended in the changeover multiplied by the number of workers multiplied by their hourly rate:
(Hours down) x (Number of staff) x (Labor cost per hour)
Product Cost – Changeover time impacts the total production for the week or day counted. Product cost is the unit price multiplied by the total items usually produced during the changeover hours multiplied by the hours down:
(Unit price) x (Standard production rate) x (Number of hours)
Recovery Costs – This includes any maintenance that extends the length of the changeover. It also consists of any maintenance time spent changing gears, pulleys, etc., required for the next run.
Changeovers may be minor (for example, a color or mix change on the fly) or significant (for example, a complete cleaning and resetting of major machine components). The key to measuring changeover time is to include accurate times for all tasks and functions.
The most accurate way to measure change over time is to use a machine data platform. This eliminates data entry errors, enables operators to document changeover procedures quickly, and lets managers focus on reducing times for each category using real-time data.
The Advantages of Reducing Changeover Time
There are numerous advantages to reducing changeover time in manufacturing, mostly tied to the fact that if changeovers are not occurring, machine can be running. These include:
-
Lower Manufacturing Costs: More value-added capacity can be unlocked because the equipment is idle for less time.
-
Smaller Batch or Lot Sizes: Reducing changeover time enables companies to reduce batch sizes and efficiently produce single-piece lot sizes.
-
Reduce Inventory and WIP: Equipment stops and starts faster due to reductions in changeover time, reducing WIP. Because overall equipment effectiveness is increased, inventory can operate on lean principles and is closer to Just in Time (JIT) status.
-
Better Startup and Quality: Startup time is smoother when changeovers are standardized and documented using best practices. This documentation means less dial-in time is required to achieve the first good part.
-
Competitive Advantage: Companies can produce smaller quantities of products. As a result, they can offer flexibility and respond to customer demand better than competitors that require a minimum quantity. This can be especially helpful for contract manufacturers or high mix/low volume shops.
Setup Time vs. Changeover Time
There are significant distinctions between setup time and changeover time; these differences are best explained by example. Setup time usually indicates a single machine. This may be a single CNC changing from an old die to a new die or replacing machine tools in a carousel for a run using different specifications.
Changeover time applies to a broader system or group of machines. For example, a complete changeover in a CNC machine company may include drilling, milling, cutting, boring, and other value-added tasks on multiple machines or a complete production line to achieve a finished part or product. In this case, all equipment will need new setups to run the batch.
Essentially, setup time may be part of overall changeover time for a large group of machines like a production line, or it may be equal to the changeover time if it affects only one machine.
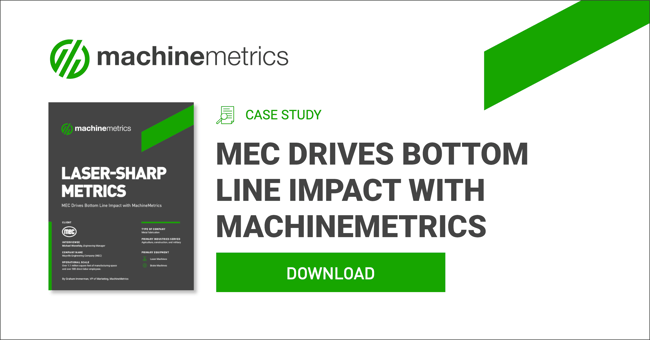
Standardized Work with SMED (Single Minute Die Exchange)
The advent of lean manufacturing saw many innovations designed to streamline changeover time and standardize the process. One of the most significant innovations heavily used in CNC machining is Single Minute Exchange of Die (SMED).
The SMED process uses clear work instructions to formalize the standard work required and reduce changeover time. This process has allowed many companies to reduce downtimes by up to 94%.
Here are the five steps used in the SMED process:
-
Identify Changeover Targets: This consists of identifying areas for improvement. Many companies start with a target of fewer changeovers.
-
Identify Changeover Elements: This includes documenting what work needs to be done and what each task will entail.
-
Separate External Elements: Many aspects of a changeover rely on things that can be done before completing the last good part. This preparation includes staging tools, equipment, staff, and other resources at or near the machine before the stoppage.
-
Change Internal Elements to External Elements: By conducting a focused process audit of the steps in the internal changeover, many process elements can be moved to the external element category.
-
Streamline: All remaining elements are examined to identify where they can be streamlined. This streamlining may include standardizing numerical settings or using jigs or fixtures to move something to its final point faster. Standard work documents specify each step in detail once the changes and improvements have been made. Audio or visual tools may also help guide those responsible for the changeover.
There is another significant piece to this puzzle: accurately tracking changeover times. Attempting to do this manually is likely to lead to delayed, inaccurate data that is difficult to process and analyze. Not to mention the amount of time operators will be required to spend manually documenting everything.
By autonomously tracking manufacturing process data with a machine data platform like MachineMetrics, continuous improvement managers and engineers can get instant insight into changeover, setup, and other KPIs.
Not only will this help to establish accurate benchmarks as well as set realistic expectations, but it will identify which continuous improvement initiatives to pursue and how effectively they are working.
Start Reducing Setup & Changeovers
Top 10 Methods for Reducing Changeover in Your Workplace
Minor improvements in changeover time can add several days of capacity to a company’s availability. Huge improvements can add weeks or months to that capacity.
Manufacturers will realize many benefits by focusing on a few methods when conducting a SMED analysis and creating a standard process for changeover times. These best-practice methods include:
-
Making Use of Checklists: Yes, checklists are old school. But in the initial stages of an improvement process, they can be a powerful way to keep track of what needs to be done. They prevent team members from forgetting tasks.
-
Repairing Broken Equipment: This applies to gauges, tools, and production machines. It may be necessary to repair a machine to its optimal running state to achieve a lower changeover time.
-
Keeping Up with Current Events: Data is essential. Ensuring that you have the correct program numbers, setting and operating instructions, machine settings, and more will mean that standard work documents match reality and good parts will be produced.
-
Using Cheat Sheets to Share Information: In companies such as CNC machining manufacturers, operators may keep a formal log of knowledge they use to work efficiently. Many of these tricks and tips can be formalized in the work instructions and shared with all operators.
-
Enhancing Homemade Work Aids: Because they operate the machines every day and are skilled in machining, many operators have made homemade jigs and fixtures. These tools lift, position, hold, or align elements within the changeover to reduce task time. These tools can be enhanced and used across the shop floor.
-
Increasing Changeover Crew Size: Manufacturing equipment can be large and require the employee doing the changeover to work on both sides of the machine. As a result, changeover time will be increased. By analyzing these steps in the improvement process, companies can identify the total labor required and reduce the changeover time by having two or more people work together.
-
Not Economizing on Tooling: Many companies skimp on tool holders to save money. This frugality results in the manual unloading and loading of holders during setup. With multiple tool holders, these tasks can be moved to external changeover elements. This makes the step “plug and play” and reduces changeover time.
-
Realizing When No Changeover is Best: For specific volume-produced parts, it may be possible to dedicate a machine to run with particular parts continually. It may also be possible to group jobs requiring a small number of machine tools into a machine with extra tools in its tool holder.
-
Not Messing Around: One of the most potent aspects of standard work is that everyone does the same job in the same way. Left on their own, staff doing a changeover may have things such as screw torques, turns, etc., that are based on “feel.” By using standard work, these tasks are streamlined and standardized.
-
Getting Rid of Hand Tools: Many changeovers require specialized screws such as Allen heads or star drives. By using hand twists and quarter turn fasteners, work speeds up.
Use Data to Visualize Your Shop Floor and Reduce Changeover Time
MachineMetrics autonomously collects data across all equipment, standardizes the information into a common model, and visualizes the data in reports of the daily production process and in dashboards to enable actionable insights. Further, historical data can be used to accurately assess production performance, such as establishing benchmarks for your most important metrics.
When it comes to increasing efficiencies, such as reducing changeover time, identifying hidden capacity, or responding faster to downtime events, MachineMetrics helps manufacturing leaders identify the most lucrative opportunities so that continuous improvement initiatives can be prioritized correctly.
Want to see it in action? Book a demo with our team today.
Want to See the Platform in Action?
Comments