Most companies place a high value on the ability to increase production capacity. And it’s especially valuable to do so if added equipment costs can be avoided. After all, the nature of manufacturing is to produce goods, and modern operations are only getting more efficient at doing so.
What is Production Capacity in Manufacturing?
Production capacity is the maximum output that can be achieved in the production process of manufactured goods. It’s generally a part-based metric that identifies the most goods that can be created given a set amount of resources (time, labor, materials).
For example, in one week a facility might produce 500 widgets.
The ideal for any manufacturer is to operate at full capacity. This means all equipment is used at the highest percentage and operates with optimized processes to incur no unnecessary downtime. However, capacity in most manufacturing companies is constrained by one of several factors.
Before we can work to increase capacity in production, it’s best first to understand how capacity is hindered via these losses.
The Six Big Losses in Production Capacity
Developed in Japan in the early 70s, the Six Big Losses represent the categories that alone or in combination can constrain production capacity. The cumulative impact of these losses defines a machine’s Overall Equipment Effectiveness (OEE) and the amount of available capacity for that piece of equipment or the factory.
The six losses are broken down into three categories with sub-categories:
Availability Losses
Performance Losses
Quality Losses
Calculating Capacity in Production
Before a company can begin to address issues caused by the Six Big Losses, it must first calculate the factory output rate. The vast diversity of industries and processes means that there will be differences from company to company. However, while measuring capacity in production is crucial, the basics of calculating capacity are the same.
-
Machine-Hour Capacity: This is a straightforward calculation of the number of machines multiplied by the number of hours available to run. This may range from single-day shifts to continuous operations.
-
Output Capacity of One Product: Here, the amount of time required to produce one unit is divided by the machine-hour capacity.
-
Manufacturing Potential of Multiple Products: Most factories produce more than one product. In this case, each product is calculated as it would be for a single product, then added to the output of the other product. If the time to produce each item is different, then the combination of units per hour up to the maximum capacity is determined by order position, or schedule, to work within that capacity.
Once the capacity is known for all equipment, the impact of the Six Big Losses will result in a utilization level for each machine and the factory. Increasing production capacity means understanding and managing those variables favorably. This is done by combining metrics that help define the utilization rate and the gap required to address it and improve.
The Production Capacity Formula
Calculating capacity for a factory, machine, or department requires straightforward formulas that calculate the machine-hour capacity and manufacturing potential for one product and multiple products.
The formula for Machine-Hour Capacity is:
Machine Hour Capacity (MHC) = No. of Usable Machines X Hours Available to Employees
You can calculate the factory output rate for one product using the values from the machine-hour capacity formula. The formula is:
Production Capacity = Machine-Hour Capacity (MHC) / Hours to Produce One Product
After calculating the capacity of each product, you can calculate the factory output rate for multiple products as a sum:
Capacity for Multiple Products = (Amount Product 1 X Hrs. to Produce Product) + (Amount Product 2 X Hrs. to Produce Product)
Once the formulas indicate overall capacity requirements per product, a factory’s capacity can be determined across multiple iterations. These include:
Want to See the Platform in Action?
Why Increase Production Capacity?
Companies seek ways to increase capacity for various reasons. This may be to meet actual increases in demand or planned increases in demand. They may also be used for short-term and long-term spikes in demand as well. Regardless, several basic strategies help companies develop a production capacity calculator to increase production capacity and optimize a manufacturing plant to take on the extra load. Accurate manufacturing capacity planning prepares companies for the future.
Short Term
-
Use Current Equipment: Using current equipment, more may result in overtime, including weekends or nights. It may also mean adding shifts in manufacturing plants that don’t have a continuous operation.
-
Outsource: This essentially uses someone else’s equipment to manufacture a part or all of a product. However, this may cost manufacturers a premium.
Long Term
-
Optimize Equipment Utilization: This means deploying tools and methods to improve the performance of existing equipment to “unlock” hidden capacity.
-
Purchase Additional Equipment: Ideally, purchasing new equipment is considered when existing equipment is optimized and at its maximum capacity. If this is the case, justifying such a significant capital expense will be far easier.
Factors Influencing Production Capacity
Finding the best ways to increase production capacity requires a clear understanding of the factors underlying it. Production capacity depends on a wide range of factors, both within and beyond your organization's control. Addressing these factors will help your team increase production capacity and maintain consistency.
Workforce Skills
You count on a skilled workforce to maintain production efficiency. Operators require the proper training to effectively run their machines and make the best use of the tools available. You should ensure that your entire team has the required training to troubleshoot issues, reduce setup times, and follow standardized workflows.
Supply Chain Reliability
Even if all of your machines are ready to run at 100%, you can still find your production constrained by supply chain issues. Disruptions, whether delays, shortages, or quality standards issues, can quickly bottleneck your production. Establishing reliable supplier relationships and improving inventory forecasting can help increase production capacity in this area.
Machine Utilization
There are a variety of machine metrics you should be carefully monitoring to ensure production efficiency. Uptime, efficiency, workload distribution, maintenance issues, and more can impact utilization and lower the capacity utilization rate. Implementing the right monitoring solution can overcome these challenges and maximize OEE.
Production Flow
Bottlenecks are among the biggest threats to production capacity. Just one bottleneck can grind production to a halt. Focusing on job sequencing, workstation layouts, material handling, and other aspects of production flow can help avoid bottlenecks. Real-time monitoring further supports these efforts to achieve uninterrupted operations.
Metrics for Increasing Manufacturing Capacity
Short-term increases run the risk of being expensive and even dangerous. If the run lasts longer than planned, overtime becomes a drag. And by outsourcing, there is always a chance of competitors attempting to copy your product. But long-term increases can be achieved that lowers cost and protects companies from the risk of duplication.
The key to unlocking hidden capacity is using best-in-class manufacturing production software and devices designed to capture, analyze, and contextualize data so that leaders can better understand and improve their operations' performance. By benchmarking progress, manufacturers can automate their production capacity calculator and processes to begin to fully optimize their equipment utilization and uncover paths for improvement.
Let's discuss a few of the key metrics management should pay close attention to when attempting to increase production capacity.
OEE
The gold standard for production capacity analysis is Overall Equipment Effectiveness (OEE) and considers availability, performance, and quality.
Ultimately, OEE measures how well you use your manufacturing equipment and identifies areas that can be improved, whether that be the amount of idle or downtime a machine experiences, the time it takes to create a part, or the extent of quality issues experiences.
MachineMetrics comes with an out-of-the-box OEE report and provides the option to create a customized report as well. You can easily segment the data to spot inefficiencies and trends.
The OEE Report comes out of the box with MachineMetrics, giving you access to OEE across each machine, group of machines, or the entire shop floor.
Further reading:
TEEP
Another production capacity analysis tool takes OEE one step further, TEEP considers maximum availability to be all available time, as in 24 hours a day, 365 days a year. In contrast, OEE uses total operations time as the maximum amount of availability, considering unscheduled time.
As you can see in the above report, you can also track TEEP within MachineMetrics.
Utilization
Broadly defined, utilization is the percentage of available production time during a selected time period that a machine was operating to process materials.
Machine utilization data may be presented in the MachineMetrics Utilization Report for the following utilization-related components:
-
In-Cycle: Percentage of the selected production time period that the machine reported to MachineMetrics as being in-cycle.
-
Spindle-Rotating: Percentage of the selected production time period the machine reported to MachineMetrics that its spindle was rotating.
-
In-Cut: Percentage of the selected production time period the machine reported to MachineMetrics that it was cutting material.
Furthermore, you can view utilization across all machines, for a group of machines, and even for individual machines, allowing you to break down the data to find overarching trends or issues with individual machines that may be impacting production capacity.
Below is a quick introduction video to the MachineMetrics Utilization report:
Further reading:
5 Steps to Increase Production Capacity
Increasing capacity to meet customer demand is a complex process. Here are some ways to achieve it:
1. Reduce Downtime
Downtime impacts everything a factory produces, including factors like raw materials management, human resources, scheduling, etc. Reducing downtime frees up total factory capacity to better meet service level requirements.
Downtime should be categorized as part of a process improvement strategy. These improvements will reduce downtime, improve efficiency across production lines, increase the number of production units per hour, and increase total factory capacity.
2. Increase Employee Hours
The most common approach for an immediate or short-term increase in total factory capacity is overtime for workers. This strategy may be viable in seasonal manufacturing or during disruption. But over time, it can become expensive.
An alternative is to add an additional straight-time working shift, assuming the operation isn’t already a 24/7 facility. Here, an estimate of future financial performance may indicate that the required shifts will be sustained over time with new demand.
However, adding overtime and additional shifts assumes that factory average efficiency is optimized and that the manufacturing process has already undergone process improvement to maximize actual output per hour. Extending hours or shifts with inefficient processes is costly and doesn’t increase machine capacity.
3. Evaluate Vendor Capacity
Most companies in the manufacturing industry tend to look inward when considering capacity, but a vendor’s own capacity can impact yours, too. Vendor quality problems can hinder your capacity by reducing total first-quality production units and requiring more inspection.
Shipment of the wrong parts or raw materials will have a similar impact. Late shipments will idle your equipment until expedited measures are taken to receive goods. A vendor evaluation can have a significant effect on your capacity.
4. Improve Internal Processes
Like reducing downtime, improving internal processes will drive greater throughput and labor utilization. Two traditional process improvement methods are Lean and Six Sigma, both of which focus on efficiency, reducing waste, and continuous improvement.
These are still good improvement strategies but are best implemented using a machine data platform. Real-time data and analytics can ramp up Lean improvement strategies, unlocking hidden capacity for the entire production process.
5. Use a Machine Data Platform
The best way to increase capacity is with a machine data platform. All the above steps can be consolidated into a single platform driven by real-time data and advanced, cloud-based analytics. Results are dynamic, and improvement success is immediately measurable. Capacity can be continually measured to unlock machine capacity across the shop floor.
A machine data platform will utilize digital technology to calculate capacity. With real-time machine data and advanced analytics, you will know exactly how much capacity is available to you at any time, using any schedule or product mix.
Case Study: Unlocking Millions in Production Capacity
By using real-time production captured by MachineMetrics, manufacturers can use accurate data-driven insights to address problems, improve processes, and unlock hidden capacity without expensive overtime or outsourcing. MachineMetrics’ system has successfully empowered manufacturers with ways to increase capacity in production while lowering maintenance costs, improving quality, and ensuring that Capex costs are used only when the current capacity is fully optimized.
Interested in how MachineMetrics is unlocking hidden capacity for our customers? In this video case study, OEE Director Matt Townsend of Avalign Technologies (a medical device manufacturer), shares how instant visibility into shop floor performance resulted in a 25-30% increase in OEE, a more effectively leveraged workforce, millions of dollars in increased capacity (without additional equipment), and increased throughput by reducing bottlenecks. Watch the case study now.
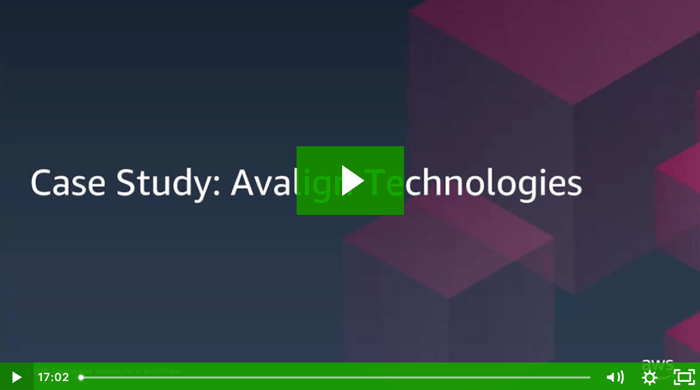
Comments